A bevonatok lebomlási feszültsége - kémiai hivatkozási könyv 21
A bevonat lebomlási feszültsége impregnálással növekszik lakkokkal (bakelit SB1-1C stb.). [C.933]
A vizsgálatok után megállapították, hogy a BH-12, BH-15, AS-8 anyagokból készült szerves szilikát bevonatok nagyon hőállóak, mechanikailag erősek és gyakorlatilag nem gyúlékonyak. A bevonatok 700 ° -ig terjedő hőmérsékletnek és nyílt lángnak való kitettségnek ellenállnak. A bevonatok száraz állapotban történő lebomlási feszültsége 30 kV / mm. A bevonatok nem változtatják meg tulajdonságukat hosszú távú, alacsony hőmérsékleten (-70 ° és alatti) és ciklikus hőmérsékleten -70 és + 300 ° között. [C.163]
Ábra. 6.12. Az EP-49A bevonat bontási feszültségének függése a vastagságtól 90 ° -os szögben és kerekítésük sugara alapján
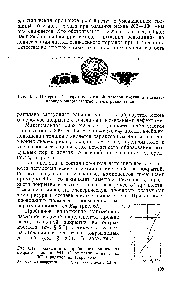
A bevonat bomlási feszültségének nagysága fontos anódos reakciók esetén. az anódizációs folyamatban előforduló és [c. 292]
Szerint a brit szabvány [1] a letörési feszültséget a bevonatok mért csatolásával a minta (eloxált csak az egyik oldalon), hogy az elektróda nyomása alatt 2,5 kg. Ezután az elektródát és annak támogatására is csatlakozik a szekunder tekercs a transzformátor, hogy az AC jellemző a lehető legközelebb a szinuszos, és egyenletesen növekvő a feszültséget 25 másodpercig, amíg a film eltörik, vagy nem lépi túl a szükséges feszültséggel. Az elektródának sima, polírozott felülettel kell rendelkeznie az érintkezési ponton, amelynek görbületi sugara 3,2 mm. A feszültségszabályozó nem torzíthatja a hullámformát több mint 10% -kal. [C.294]
Az elektromos szigetelő bevonat színe szürke és sötétszürke között változik. A bevonat vastagsága 15-120 μm. Ezt a törékenység, a magas elektromos ellenállás jellemzi. Ötvözetek AlMg, AMTS és AD1 egy fóliavastagság 60 - 100 mikron letörési feszültsége 350 - 600 V, míg a D16 és B95 ötvözetek (bevonatvastagság 40-60 m] - 300 - 400 V [c.212]
A bevonatok elektromos tulajdonságait teljes mértékben az elektromos szilárdság (meghibásodási feszültség), felületi ellenállás határozza meg. dielektromos veszteségek (belső ionizáció vagy korona által okozott veszteségek), ívállóság és ömlesztett ellenállás. Meg kell azonban jegyezni, hogy a földalatti fémvezetékek bevonatait teljesen teljesen jellemezheti az ellenállóképesség, ami szinte mindig így van. Ez a kis elektromos terhelésnek köszönhető. a csővezetékek észlelt szigetelése. Még a legrosszabb esetben is, amikor a szigetelt csővezeték rendkívül intenzív vándorlási területnek van kitéve, az áramuk, a cső-föld potenciálkülönbsége nem haladja meg a több tízvoltot. Ezért a nagy elektromos szilárdság kérdése nem jelentős a földalatti csővezetékeknél. Dielektromos veszteségek a szigetelő bevonatban. amelyet a veszteség szögének érintője alapján értékelnek, a feszültség aktív összetevőjének arányát jelenti a reaktívnak. Ez a jelző fontos a bevonatok anyagának megválasztásakor, amikor az utóbbi magas frekvencián dolgozik. Ilyen körülmények között kis dielektromos veszteségekre van szükség. Nyilvánvaló, hogy nincsen értelme ennek a paraméternek a használatára a csővezetékek bevonatainak jellemzésére, mivel ez utóbbi legrosszabb esetben csak az 50 Hz-es kóros áramlatok területén jelenhet meg. Ugyanezen okokból semmi értelme nem beszélni az ívstabilitásról, vagyis az anyag azon képességéről, hogy ellenálljon az íves ív kiürítésének. [C.53]
A 0,5 mm vastag bevonatok kezdeti jellemzői nagyon magasak. A nedvesség felszívódása néhány hónap alatt kevesebb, mint 1%, és az első 7 napban fejeződik be. A leállítási feszültség 1 mm-nél nagyobb, mint 16 kV. Az elektromos ellenállás 6,5. 10 ohm A bevonat minősége nem változik -40 ° C-ra. A megnövekedett hőmérséklet 150 ° C-ig történő tartós expozíciója nem változtatja meg a bevonat tulajdonságait. amely csak szilárdabbá válik. A bevonat állapota jó marad három év után a tenger és a csapvíz expozíciója után, 5-20% kénsav és 5-10% sósav. Az évek során a marószóda hatása nem rontja a bevonat minőségét. A bevonatban lévő buborékok megjelenése az 5% -os hidrogén-fluorid hatása után 25 napig tartható. és alumínium-hidroxidot három év után. Szerves vegyületek, például metanol, triklór-etilén hatására. metil-etil-keton. buborékok jelennek meg a negyedik napon. A nagy potenciálú katódvédelem és az áramsűrűség nem káros hatással van a bevonatra. [C.143]
Nagyon gyakori bevonatok, amelyek tartalmaznak egy AlBO3-at és egy másik fázist (Al, Ni, MgO). A plazmában hidrogént és nitrogént használnak. A részecskék diszperziója 20-60 μm. Szilikát- és foszfátüveg-mátrixot tartalmazó elektromos szigetelő bevonatok is ismertek. Ezek a bevonatok legfeljebb 3-30%> AI2O3-t tartalmaznak, nyílt porozitásuk (3-6%) és Os érték = 80-200 mPa. A bevonat vastagsága [c.219] -ig
Görbületi sugár hiányában a bevonatok lebomlási feszültsége erősen gátolt (6.12. Ábra). Az 1. ábrán látható adatok. 6.12-et a [c.110] méretű acél kockákon kaptuk,
Szilárd eloxálás. A működés közben súrlódásnak kitett alkatrészeket 170-250 g / l H2SO4-ot tartalmazó elektrolit eloxálják. Mode eloxálás elektrolit hőmérséklete a - 2 és + 5 ° C, a = 0,5 A / dm kezdeti feszültség 25 V, az utolsó 50-80 Az eloxálás 1,5-2 órán át. A hűtés a elektrolit alkalmazásával hajtjuk végre egy hűtőrendszerrel. Az eloxálás során a fürdő tápfeszültség áramkörébe tartozó reosztátok segítségével állandó áramsűrűséget kell fenntartani. A filmek legjobb minőségét az alumínium és annak ötvözeteinek nagy oxidációja biztosítja magnéziummal és mangánnal. On önthető ötvözetek Silumin-típusú letörési feszültségét oxid bevonatok 2 - 3-szor alacsonyabb, mint a kovácsolt ötvözetek B95, AB, AK4. Viszonylag alacsonyabb az ilyen fóliával bevont deformálható ötvözetek kopásállósága is. A technikai alumínium szilárd fóliának mikrokeménysége 500-520 kgf / mm. az ötvözeten AV-480 -500 kgf / mm. a D16 - 330-360 kgf / mm ötvözetből. az ötvözet AL-450 - 480 kgf / mm. [C.216]
Az üvegzománc olcsó és széles körben elterjedt anyagokból készül, legfeljebb a védett fekete fém tömegének 6% -a, és a termékeknek magasabb kémiai ellenálló képességgel rendelkezik. mint például a nikkelötvözet fém, amely a különleges acélok részeként található. A saválló üveg-zománc bevonatok rendkívül ellenállnak az ásványi és szerves savak forró oldatainak. sók, savas korrozív gázok és gőzök széles hőmérséklet- és koncentrációtartományában. A hagyományos saválló zománcok ellenállnak a forró lúgos oldatoknak, akár 5% -os koncentrációig. Különleges kislotoschelocheustoychivoe bevonatban Ukrán NIICHIMMASH, lehet működtetni mind savak és a forráspontja oldatok maró alkálihidroxid-koncentráció 10% alkálifém-karbonátok és a koncentrációt 40%. A zománcok megengedett üzemi hőmérséklete folyékony közegben 150-200 °, gázfázisban pedig 500-700 °. Az acél zománcberendezések fagyállósága elérte a 70 ° -ot és az öntöttvas 30 ° -ot. A zománcburkolatok elektromos szilárdságát 10-25 mm-es lebontási feszültség jellemzi. [C.150]
Ami a bontási feszültség kérdését illeti. akkor a bevonatok esetében elegendő az értéket 40-60 kV1 mm-re korlátozni (még akkor is, ha az érzékelők szigetelésének folytonosságát vagy hibakijelzőit 50 kV-ig működtetik). [C.53]
Ezen eszközök használatakor figyelembe kell venni a teszt bevonat szikrájának meghibásodásának veszélyét, mivel nagyfeszültségű áram kezelésére van szükség. Annak érdekében, hogy elkerüljük a lebomlást és következésképpen a bevonatok károsodását, legalább hozzávetőlegesen ismerni kell a korróziógátló vagy tömítő anyag lebomlási feszültségét, és nem szabad megengedni a feszültség növekedését a határértékekre. Tehát például a saphenapolén-naynitovyh bevonatok vizsgálata során a bevonat vastagsága több mint 0,7 nm vastagságú legyen. Az UT-32 tiokolid tömítőanyagból történő bevonáshoz ez az érték 3 kV1 mm-ig terjedhet, és a CL típusú polisziloxán vegyületek esetében akár 15-17 kV1 mm-es feszültség is biztonságban lesz. [C.13]
Lásd azokat a lapokat, amelyeken a "Bevonatok meghibásodási feszültsége" kifejezés szerepel. [c.933] [c.189] [c.48] [c.280] [c.165] [c.261] Festékbevonatok kémiai és technológiája Izd 2 (1989) - [c.0]