Ironizálás (egyébivanie)
Vasalásnál olcsóbb elektrolitokat, oldható anódokat használnak a krómozáshoz képest. Ebben a folyamatban nagyobb áramsűrűség használható. A csapadék áramlási sebessége 85. 90%. A folyamatot jóval rövidebb időtartam és költség jellemzi, és lehetővé teszi nagyobb alkatrészek kopásállóságának (oldalanként legfeljebb 1,5 mm-es) helyreállítását. A vasalás sebessége magasabb, mint a krómozásnál, mert a vas elektrokémiai egyenértéke 1,042 g / Ah, a króm 0,324 g / Ah.
Amikor ostalivanii lehetséges bevonatok, amelyeknek elég nagy keménységű (3000. 7000 N / m 2) és kopásállósága edzett acél nem alacsonyabb, mint 45. Ezek a pozitív oldalon magyarázza annak széles körű használata a javítási gépek. bevonat tulajdonságai függnek az alkalmazás módjától.
Keménység elektrolitikus vas kicsapódása csökkenésével növekszik sókoncentráció az elektrolit, az áramsűrűség növelése, csökkentik EVAP-ry, adagoljuk különböző szerves elektrolitokat és ásványianyag-kiegészítők (ábra. 57).
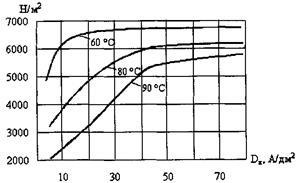
57. ábra - A hőmérséklet és az áramsűrűség hatása a mikrokeménységre
Az alacsony szén-dioxid-kibocsátású acéllemezeket az anitoként használják a többiivanii számára. A gyártási körülmények között az elektrolit-klorid előállitását a sósavban levő alacsony széntartalmú 20 acélból történő maratással hajtjuk végre. A katód és az anód felületének arányát 2: 1 értéken kell tartani. A rész egységes bevonatát az anódok katódok (részek) alakításával biztosítják.
A sűrűség sima növekedése a nulla értékről a technikai feltételek által meghatározott értékre vonatkoztatva az 5. 10 percben lehetővé teszi a csapadék jó tapadását az alapfémhez.
Hogy előkészítse a klorid elektrolitot alkalmazunk vas-klorid FeC12 • 4H2O, kis mennyiségű sósav HC1, és néhány más komponensek, mint például mangán-klorid MPS12 • 4H2O, nikkel-klorid NiC12 • 4H2O, amelyek be, hogy javítsa a tapadást és kopás-csont. A katódon hidrogén, kivéve a vas kicsapódik, és belép a kristályrácsba a csapadékot, növelve annak ridegség és a tendencia, hogy állítsa. Alacsony hőmérsékletű megeresztés (200 ° C 150.) nem tud a belső-konjugáció, és magas hőmérsékleten (450 ° C), bár ez pozitív hatást gyakorol a kifáradási szilárdságot (növeli), de csökkenti a kopásállóság bevonatok.
A ferri-klorid koncentrációja az elektrolitban 200 és 700 g / l között változhat. Az alacsony koncentrációjú elektrolitok 200-220 g / l ferri-kloridot tartalmaznak. Lehetővé teszi nagy keménységű, de kis vastagságú (0,3-0,4 mm) betétek beszerzését.
Az elektrolit nagy koncentrációjú (650 és 700 g / l FeC12 • 4H2 O) ad egy kosár-elérésének esélyét bevonatok vastagsága nagyobb, de kisebb a keménysége. Nai szélesebb körben elektrolitok Átlagkoncentráció-tartalmazhatnak-tartalmú 400 g / l FeC12 • 4H2O, 2 g / l HC1 és 10 g / l MPS12 • 4H2 O. Ez az elektrolit-IME nagy kimeneti áramot, és biztosítja a jó mechanikai tulajdonságok felfedezést.
Annak érdekében, hogy minőségi bevonatokat kapjunk a többiivaniya folyamat intenzív áramlásával, nem helyhez kötött elektromos rendszereket használunk.
A javítás során gyakorlatilag fémes lerakódás fordított, aszimmetrikus és impulzusos áramokra utal.
Az acél fürdőkben történő bevonáskor a bevonatokat külső lineáris átáramlású másivaniya segítségével kell bevinni. A fürdők gyártásához antiklórit-acélok és néhány króm-nikkel-acél alkalmazása magas hőmérsékleten elektrolit-kloridokkal jól működik. A többiivaniya fürdőket phaolitból, vinyi rétegből és titánból is készítenek.
A nagyméretű testrészeket extra-hiúsági módszerrel helyreállítják.