Szupervízelés - stadopedia
A csiszoló rudakból áll, amelyek nagy frekvenciájú és kis ütemben rezgő mozgást végeznek a forgó rész felszínén.
Alkalmazható külső és belső hengeres felületek kezelésére.
A finom, finom szemcsés csiszolórudakat a munka során rugókkal vagy hidraulikus eszközökkel préselik a feldolgozott felületre.
Mivel a hűtőfolyadék kerozint használt olajjal.
A feldolgozási támogatás nem maradt fenn.
Az eljárás a kagylók eltávolítását jelenti a fennmaradó részek felületéről az előző kezelésből.
A lehúzást olyan csiszolással végezzük, amelynek felületén finom szemcsés csiszolópépet keverünk zsírokkal vagy pasztával.
A sziklakert lehet öntöttvas, acél, bronz, ólom. Mivel a csiszolóanyag a szilícium-karbid porát használja, a gyémántpor, az elektrokorrundum csiszolt.
Mint paszta, használjon króm-oxidot, alumínium-oxidot.
A feldolgozásra jutó juttatás 0,005-0,02 mm.
Kivágott, finomszemcsés rudakkal ellátott fej, szegmensek.
A fej forog és elmozdul a mozgó részen kívül.
A szerszám nagy vágási tulajdonságait a következők biztosítják:
1. az instrumentális anyag helyes megválasztása
2. Optimális szerszám geometria
3. Megfelelően végzett hőkezeléssel (az eszköz keménységet és kopásállóságot biztosít)
4. A szerszám működési feltételei
Számos módszer alkalmazható, amelyek lehetővé teszik a szerszám vágó részének ellenállását további műveletek végrehajtásával.
a) a műszer felszíni rétegének telítettsége (uralkodás, króm, szulfidáció)
b) a hőkezeléssel szembeni ellenállás növelése a szerkezet javításával (hideg kezelés, gőzölés)
5. A készülék felülete minőségének javítása (hibakeresés, lapozás)
A Zanirovanie egy kemoterápiás folyamat, amely az acél felületi rétegének telítettségét jelenti szénnel és nitrogénnel bizonyos hőmérsékleten történő diffúzióval.
A folyékony kvaternion alacsony hőmérsékletű.
Gáz és száraz cianidáció van.
A szulfidáció a fém felületi rétegeinek kénnel való telítési folyamata, a felületen képződött kénvegyület csökkenti a súrlódási együtthatót és növeli a kopásállóságot.
Az eljárás 550 ° C-os hőmérsékleten történik a fürdőben ≈ 40-90 perc alatt.
A szerszám tartóssága 1,5-2-szer nagyobb lesz.
Króm - acél, bronz galvánfürdőben.
A réteg vastagságát két milliméter századra állítjuk be.
Szerszám: broaches, dolby.
A gőzölés folyamata.
Eszköz bronzból, acélból.
1. öblítés forró vízzel
2. mosás 70% -os szóda oldatban
3. Expozíció 15-30 perc. elektromos kemencében, 400 ° C-ig terjedő hőmérsékleten.
A kemencét vízgőzzel öblítik, és 560 ° C hőmérsékleten 30-40 percig tartják. Ezután a lehűtött anyagot fűtött olajban 50-70 ° C-ra leeresztik, 0,05 mm oxidréteget képeznek a szerszámon.
A erősség felére nő.
Fémek nyomáson történő feldolgozása.
A fémformák fő típusai: hengerlés, préselés, rajzolás, kovácsolás, sajtolás.
Gördülő. Hengerlés közben melegített vagy hideg munkadarabok folynak a gördülőmalmok forgó gerendái között.
Háromféle gördülő típus létezik: hosszirányú (profilos és alakú profilok), keresztirányú és keresztirányban csavaros (forradalmi testekhez). A hosszanti hengerlésnél a gerendák különböző irányú elfordulást és deformálódást okoznak a munkadarabon. A keresztirányú sugarak egy irányban forgathatók.
A préselés egy olyan fémes eljárás, amely olyan nyomással működik, amelynél a fém egy nyíláson keresztül kinyomódik egy zárt üregből, és ennek eredményeképpen egy olyan tárgy van, amelynek nyílással ellátott része van.
Kétféle sajtolás létezik: közvetlen és hátra.
Rajzolás - a munkadarab külső erőinek (rendszerint hideg állapotban történő) húzása alatt áll egy nyíláson keresztül, amelynek keresztmetszete kisebb, mint a munkadarab kezdeti szakasza.
Kovácsolás - műanyag állapotban történő fémmegmunkálás, statikus vagy dinamikus nyomás.
A kovácsolási műveletek közé tartozik az áteresztés, az iszap, a hajlítás, a lyukasztás vagy lyukasztás, a fakitermelés stb.
A bélyegzés a fémek feldolgozása bélyegek segítségével történik. Nagy teljesítmény. A sajtolás lehet meleg és hideg, normális és leveles.
A porlasztás az egyik olyan módja a felületkezelésnek, amelyet az ipari vállalatoknál használnak speciális kezelésként.
A permetezés fő célja a korrózió elleni védelem, a kopott felületek, gépalkatrészek és szerszámok javítása.
A plazmafúvók használatával, a robbanás energiájával és más jelenségeken alapuló porlasztás új módszereinek kialakítása lehetővé teszi olyan anyagok bevonását, amelyek nem használhatók.
A spray számos tulajdonsággal alkalmazható. Lehetőség van porlasztani: hőálló, hőszigetelő, kopásálló, korrózióálló, elektromos szigetelő és egyéb bevonatok.
Nagy teljesítményű gépek, készülékek és szerszámok létrehozásakor a probléma elsősorban olyan anyagok előállításához szükséges, amelyek ellenállnak a kemény munkakörülményeknek.
A porlasztott anyag megolvasztására használt hőforrás típusával a szóróberendezés meglévő tervei alapvetően kétféleképpen oszthatók meg: gázláng és elektromos.
A gázláng berendezésben az éghető gáz + oxigén keverék égése során felszabaduló hőt használják.
Az elektromos berendezés az elektromos ív hőjét használja.
A legszélesebb körben alkalmazott módszer a gáz lángszórásos eljárás, amelyet nikkel és kobalt alapú ötvözetek, kerámia és egyéb tűzálló anyagok bevonására használnak.
Különleges típusú lángszórás a permetezés, amely az acetilén és oxigén keverékének detonációs energiáját használja fel.
A robbanás robbanás gyorsan áramló reakciója.
Ez a fajta permetezés lehetővé teszi a még nagyobb olvadáspontú anyagokból származó bevonatokat.
A porlasztás elektromos típusai közül a legrégebbi az elektromos íves fémezés módszere.
Korábban egy íves égést használtunk egy váltakozó árammal, ami nem engedte meg, hogy stabil permetezési folyamatot érjünk el.
Most, hogy megkapja az ívet, egyenáramot használnak, ami jobb működésstabilitást biztosít.
Az elmúlt években olyan plazma permetezőket és berendezéseket használtunk, amelyek nagyfrekvenciás indukciós permetezést használnak, és lehetővé teszik minden anyag permetezését.
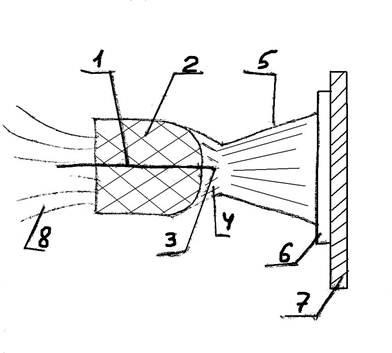
2 - égés során keletkező láng
3 - a huzal olvadáspontja
4 - légáramlás
5 - fémrészecskék
A hőenergia forrás láng, amely az oxigén + éghető gáz (acetilén) keverékének égéséből ered.
A porlasztott anyag állapotától függően a porlasztás lehet vezeték, rúd és por.
A drót és a rúd permetezése elve ugyanaz.
A huzal vagy rúd formájú permetezett anyagot az égő központi lyukán keresztül tápláljuk és a lángban megolvasztjuk.
A sűrített levegős sugár az öntött anyagot apró részecskékre permetezi, amelyeket a kezelendő felületen helyeznek el.
A huzaláramot állandó sebességgel állítják elő az égőbe beépített légturbinával hajtott hengerek, amelyek sűrített levegőn vagy elektromos motoron működnek, és a turbina vagy a motor forgási sebességének pontos beállítására van szükség.
Egy villanymotorral ellátott égő lehetővé teszi a vezeték etetésének pontosabb szabályozását és állandó sebességének fenntartását, de nagyon nehézkesek.
A sodrott huzal átmérője 3 mm, alacsony olvadáspontú huzalok (Al-Zn) Ø 7 mm-ig.
Poranyag lángszórás.
A porlasztott por bejut az égőbe, felgyorsul a szállítógáz (O2 + éghető gáz) áramlásával, és kilép a fúvókából a lángba, ahol felmelegszik. A forró gáz forrása belekapaszkodik a por részecskéibe, és a permetezett felületre vonatkozik.
A porégőkben, mint a huzalégőkben, a permetezett anyagnak a lánggal való ellátásához és a megolvasztott részecskék felgyorsításához sűrített levegő sugárral lehet előállítani. Ugyanígy a műanyag is permetezhető.
A gyulladásgátló bevonatok nem alkalmazhatók lángszórással.
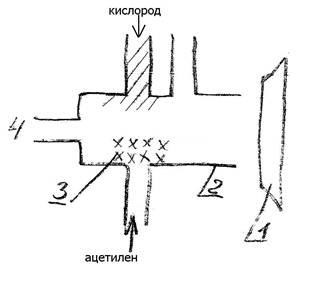
Detonációs permetezés - kemény kopásálló bevonatok készítésére szolgál.
2 - hűtött hordó
O2-ot és acetilént (C2H2) a kamrába szigorúan meghatározott mennyiségekben szállítanak. A hordó az alkatrészhez van vezetve. A kamrában lévő különleges lyukakon keresztül a nitrogén elpusztítja a porlasztott anyag porát.
A gázkeverék, amelyben a szuszpendált állapotban porlasztandó por elektromos szikra meggyújtja, robbanás következik be. A robbanás következtében a hő felszabadul és hullám alakul ki, amely felmelegíti és eloszlatja a porrészecskéket.
Ezzel a módszerrel nagy mennyiségű kinetikus energiát jelentenek a por részecskéi számára. Az éghető gázok keverékének robbanása után a hordót nitrogénnel fújják az égési termékek eltávolítása céljából.
A permetezés elektromos módszerei.
Két elektróda folyamatosan táplálódik a elektrometallizáló berendezésbe. Ezeknek a vezetékeknek a végei között elektromos ív van.
A elektromágnesesítőben. amelyen keresztül sűrített levegőt szállítanak. A sűrített levegő áramlása az elektródákból megolvadt fémrészecskéket szétszakítja, és a permetezett felületre szállítja.
A elektrometallizátor mind egy állandó, mind váltakozó árammal működhet.
A váltakozó áram használatakor az ív nehezen ég, és nagy zaj mellett égő, folyamatos áramerősség mellett működő, a permetezett anyag finom szemcsés szerkezetű.
A permetezés hatékonysága magas.
0,8 mm-es porlasztó vezeték esetén; 1; 1,6 és 2 mm.
Az ívmódszer előnyei:
1. Nagy teljesítményű folyamat.
2. A folyamatidő jelentősen csökken.
3. Több tartós bevonat keletkezik, amely jobban kombinálható a hordozóval, mint a gáz lángszórással.
4. Az elektródáknál különféle fémekből álló drótot lehet bevinni, így bevonatokat nyerhetnek az ötvözetükből.
1. a porlasztott anyag túlhevülése és oxidációja.
2. A permetezett ötvözetben lévő ötvözőelemek kiégése.
Ha a gáz, amelynek molekulái több atomból állnak, 1000 ° K-ot meghaladó hőmérsékletig, felmelegszik, a molekuláris kötések lebontásának folyamata megtörténik, és a gáz atomos állapotba kerül (a disszociáció bekövetkezik). Ennek a folyamatnak a hőmérsékletét a gáz típusa és a nyomás határozza meg.
Olyan gáz, amelyben az atomokat vagy molekulákat ionizálják, plazmának nevezik.
A plazmának nagy a vezetőképessége.
Jelenleg kétféle típusú égőt használnak az iparban a plazma előállításához: plazmavágó és plazmavágó égők.
A plazmavizsga eljárással kapott bevonatok nagy sűrűséggel és jó tapadást mutatnak a hordozóhoz.
A plazmavizsgálatnak azonban gyenge teljesítménye van, zajjal és erős ultraibolya sugárzással jár.
Ennek a módszernek a hátrányai közé tartozik a berendezés magas költsége és működési költsége.