A korszerű technológiák a gáz-hőszigetelő bevonatok megszerzéséhez, fémkereskedelmi portál
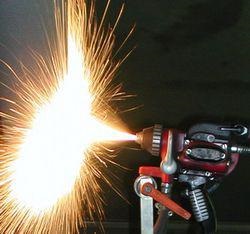
A gázt termikus permetezés modern, jól kidolgozott módszerek komplexumaként alkalmazza a legszélesebb anyagcsalád funkcionális, regeneratív és dekoratív bevonatait.
Alkalmazási területe rendkívül kiterjedt - a sugárhajtású motoroktól és a forgattyús tengelyektől az orvosi implantátumokig és a kerékpár felnikig.
A termikus fémszórás (Thermal permetlé) megérteni egy sor folyamatok, amelyekben a permetező anyagot megolvasztjuk, diszpergáljuk (porlasztott), és átvittük a felületre útján gáz jet. A hatást a felülettel, a részecske permetezés anyag lehűl azonnal (a sebesség a hűtés elérheti egy millió fok másodpercenként), és van deformálva szorosan illeszkedő vele. Emiatt a gáz-hőszigetelő bevonatok szalagot vagy sík finomszemcsés mikrostruktúrát tartalmaznak. A bevonat tartalmazhat pórusokat is, és fémek porlasztása esetén az oxidok és nitridek részecskéit.
A permet lehet fémek és ötvözetek, valamint nemfémes vegyületek, karbidok, oxidok, szemüvegek, kerámiák és polimerek, valamint kompozit anyagok. Elvben ez a módszer permetezhet bármilyen olyan anyagot, amely nem bomlik le a melegítéskor az olvadáspontra. Aljzat szerepében fémek, kerámiák, fa vagy műanyagok működhetnek.
A gáz-hõ bevonatok alkalmazását az iparágban körülbelül 100 évig gyakorolták, de az elmúlt húsz évben jelentős változások zajlottak le ezen a területen, amelyek az új technológiákat új képességekké teszik. Az ilyen változásokat a technológiai berendezések és a nyersanyag-termelés technológiájának javítása okozta a porlasztásnak, az új automatizálási rendszerek bevezetésének és a minőség-ellenőrzésnek.
A gáz-termikus permetezési módszer feltalálója Max Ulrich Schop volt. A porlasztott ólom helyhez kötött tégelyes üzemével különböző anyagokat kapott bevonatokat. Zürichben 1909-ben alapított technológiája alapján fémezõ üzemet nyitottak meg. 1913-ban, Ulrich g. Shoop javult, és szabadalmaztatott kialakítás láng szórópisztoly, ahol az anyag a permetezés van betáplálva a láng a gázégő formájában huzal. A Shoop által kapott bevonatok sűrűsége a kompakt anyag sűrűségének 85-90% -a volt. 1918-ban ő és kollégái kifejlesztettek egy elektromos ívű permetezőt, amely lehetővé teszi a fém bevonatok hatékony bevonását. A bevonatok permetezéssel történő bevitelének módját a technológia feltalálója nevezte el bevásárlással. 1921-ben Ulrich Schopp szabadalmaztatta a fém-por gázlángszórás technológiáját.
Termikus fémszórás folyamatok, hogy osztályozzák a természet a hőenergia-forrás (lásd. Ábra.) Az olyan rendszerekben, láng, nagysebességű és detonációs permetezés, az energiaforrás által termelt hő a kémiai reakció a tüzelőanyag gáz elégetése. Az ív és a plazma permetezés folyamatában az energiaforrás az elektromos ív. Gondoljunk bele részletesen a gáz-termikus permetezés minden módjára.
Égési lángszórás
Lángszórásos végezzük egy speciális égőfej, amelyben levegő befúvatásával (vagy oxigénnel) és egy éghető gáz (acetilén, propán, hidrogénatom vagy hasonló.) Az égési zóna táplálják permetezés anyagot, megolvasztjuk égő lángja permetezzük, és átvittük gázsugár a felületre. A gáz-lángszóró folyamatok viszonylag magas porozitású bevonatokat (5-12%) és alacsony tapadást eredményeznek a hordozóhoz képest. Ennek oka a gázsugár (kb. 50 m / s) alacsony sebessége. A láng hőmérséklete korlátozza az anyagtartományt, amely gázlángos módszerrel permetezhető.
A porlasztott anyag rudak, huzalok, porok vagy zsinórok formájában adagolható porlasztóként adagolható. A fémes anyagokat általában rugalmas vezetékek formájában használják, ami nagyon kényelmes és biztosítja a folyamat folytonosságát. Kerámia anyagok - porok vagy speciális szinterezett rudak formájában. A rudak használatával kapcsolatos jelentős hátrány a folyamat megszakadása.
Ha többkomponensű porokat permetezünk, a bevonatok tulajdonságainak egyenletessége, a porok szegregációjával (szétválasztásával) lehetséges. Ezt a problémát megszünteti a flexibilis köteg által elhelyezett, ugyanabból a porból álló flexibilis kötélanyagok használata. Permetezéskor a kötőanyag teljesen elpárolog, és csak a poranyag ülepszik a hordozóra.
A gáz-lángszórás fő előnyei. széles körben elosztva, a felszerelés egyszerűsége és megbízhatósága, valamint a mobilitás. Ez a módszer használható a pályán (az úton). A gáz-lángszóró technológiákat sikeresen alkalmazzák olyan alkatrészek geometriájának javítására és helyreállítására, amelyek nem komoly terheket tapasztalnak.
Plazma permetezés
Ezzel a permetezési módszerrel az energiaforrás egy elektromos ív, amely két elektróda között gyújtott. Az íves égésterületen keresztül inert gázt fújnak (általában argonnal nitrogénnel vagy hidrogénadalékokkal), ami ionizáló és plazmát képez. A íves térben a plazma hőmérséklete eléri a 15 000 ° C-ot. A lerakódott anyag porát betápláljuk a plazma sugárába, amely megolvad és átviszik a kezelendő felületre. Az íves égési zónában a magas hőmérséklet ellenére a kezelt felület nem melegszik erősen, mivel a hőmérséklet hirtelen csökken, amikor az íves területet elhagyja.
A plazma permetezés nikkel és vasötvözetek, karbidok, nitridek, boridok bevonatait eredményezi. A plazma rendkívül magas hőmérséklete lehetővé teszi az eljárásnak az alumíniumot és cirkónium-oxidokat és más tűzálló anyagokat tartalmazó tűzálló kerámiával történő szórását, amelyet más módszerekkel nem lehet permetezni.
Az előnyök a plazma permetezés is a rugalmasság, a képesség, hogy ellenőrizzék a fizikai és mechanikai tulajdonságait a bevonat és a rugalmasság, amely lehetővé teszi, hogy spray gyakorlatilag bármilyen anyagból, és ezek kombinációi, beleértve a fogadó kompozit többrétegű bevonattal.
A plazmavizsga berendezés bonyolultabb, mint a gázlángszórás, mivel gáz- és elektromos berendezést tartalmaz.
Jelenleg a plazma lerakódás új módszereit intenzíven tanulmányozzák és fejlesztik. Különösen kritikus esetekben, a nagy tapadás és bevonat sűrűség elérése érdekében a plazmát vákuumkamrában hajtjuk végre csökkentett nyomáson vagy inert gáz atmoszférában. A nyomás csökkentése a részecske sebességének növekedéséhez vezet, ami lehetővé teszi a sűrűbb bevonatok kialakulását. Az eljárás inert gáz atmoszférában kizárja a porlasztott anyag oxigénnel történő kölcsönhatását, ami lehetővé teszi a kémiailag aktív anyagok, például a molibdén diszilicid, intermetallidok permetezését. Az ilyen bevonatok magas keménységű és kémiai ellenállással rendelkezhetnek magas hőmérsékleten.
A plazmamódszer másik ígéretes módosítása az a folyamat, amelyben a sputtered anyagot egy inert gázáram veszi körül annak érdekében, hogy kizárja a sputtered részecskék oxigénnel való kölcsönhatását. Ennek a módszernek az előnyei megegyeznek az inert atmoszférában végzett eljárással.
Detonációs Gun (D-Gun)
A detonációs permetezés telepítése hasonlít egy olyan géppuska számára, amely a fűtött por egy részét tüze ki. Az oxigén és az éghető gáz keverékét a zárt égetőkamrába vezetik, amelyhez a hordó van rögzítve, és a hordó a permetezett felület felé irányul. A kamrába pasztát vezetünk be egy betápláló nyíláson keresztül. A keveréket elektromos szikra gyújtja meg és robban. A forró részecskék az égési termékekkel együtt kifutnak a kezelendő felületre. A részecskék hőmérséklete az ütközés idején 4000 ° C-ra emelkedik. A felvételek gyakorisága 3-4 másodpercenként.
A nagy részecske-emissziós sebesség miatt a robbanás során kapott bevonatok. nagy szilárdságú, kemény és kopásálló. A detonációs bevonatokat cermet bevonattal készítik: volfrámkarbidok, titán és kobalt, titán és bór-nitridek, alumínium-oxid.
A módszer hátránya a kapott bevonat heterogenitása és a technológiai berendezések összetettsége.
Nagy sebességű oxigén-üzemanyag (HVOF)
A nagysebességű permetezési technológiákat joggal tekintik a legmodernebb gáztermikus módszereknek.
Elvileg a HVOF módszerei nem különböznek a gázlángtól, azonban az égő tervezési jellemzői miatt nagyon magas permetezési arány érhető el bennük.
A nagysebességű permetezés ötletének számos megvalósítása létezik. Például egy kiviteli alak tartalmaz egy égéskamrát és egy hosszú hengeres fúvókát, amelyet víz hűt. Oxigént és éghető gázt fecskendeznek be a kamrába nagy nyomás alatt. Szigorúan az égő tengelye mentén adagolják a porlasztott anyag porát. Az olvadt porrészecskék és a gázégető termékek keveréke, amely áthalad a fúvókán, felgyorsul a szuperszonikus sebességre, és a szubsztrátum irányába repül. Az első generációs HVOF rendszerekben az égéstérben a nyomás 0,3-0,5 MPa volt, a részecske kibocsátási sebessége elérte a 450 m / s értéket. A kibocsátott részecskék felgyorsítása érdekében a kamra nyomását 1-1,5 MPa-ra növeljük, és a Laval fúvókát a pisztoly szerkezetében fecskendezzük be. A részecskék kibocsátási sebessége ebben az esetben meghaladja az 1000 m / s értéket.
A nagysebességű eljárással kapott bevonatokat olyan sűrűségi értékek jellemzik, amelyek a kompakt anyag sűrűségének 99% -át és a maradék feszültségek alacsony szintjét érik el. Mivel az utóbbi jelenléte a bevonat vastagságát korlátozó fő tényező, a HVOF porlasztás lehetővé teszi a sokkal nagyobb vastagságú bevonatokat a lángszóráshoz képest. A teljesítmény jellemzői mellett a nagysebességű bevonatok jobbak, mint a robbanásszerű permetezéssel nyertek. Számos alkalmazásban a HVOF fokozatosan fokozza a plazma lerakódását.
Tekintettel arra, hogy az incidensrészecskéknek nagyon nagy kinetikus energiája van, nem szükséges olvadék ahhoz, hogy kiváló minőségű bevonatokat alkosson, ami számos esetben alkalmazható ezekben a folyamatokban, például a cermetek lerakódásában.
A HVOF permetező technológiák felülmúlhatatlanok az olyan alkatrészek erőforrásainak helyreállításához és meghosszabbításához, amelyek magas korrózió-eróziós kopást és kavitációt tapasztalnak az előállított bevonatok nagy sűrűsége és kopásállósága miatt.
A fejlett országokban a nagysebességű lerakódás szinte teljesen eltüntette a vákuum lerakódás módszereit, és hagyta abba a rendkívül ökológiai galvanikus bevonatokat.
Arcíves permetezés
Az elektromos ívszórás az egyik legkedvezőbb módja a bevonatok permetezésének, az alacsony energiafogyasztás és a nagy lerakódási arány jellemzi. A fűtési forrás, mint a plazma lerakódás esetében, elektromos ív. Ebben az esetben az ív a porlasztott anyagból két vezeték között meggyullad, amely állandó sebességgel kerül a permetező zónába, és az íves övezet hőmérséklete meghaladhatja az 5000 ° C-ot. Az olvadt anyag diszpergálását és a kezelendő felületre történő továbbítását egy sűrített gáz, általában levegő sugárzásával állítják elő.
Mivel a lerakódott anyag egy elektródként működik, ezzel az eljárással csak elektromosan vezető anyagokat (fémeket és ötvözeteket) lehet permetezni, ezért néha arcíves fémezésnek nevezik.
Az elektromos ívszórás előnyei az egyszerűség, a gazdaságosság és a magas termelékenység (akár 45 kg / h).
Ezt a folyamatot széles körben használják korróziógátló cink és alumínium bevonatok felhordására a hajóépítésben, a városi infrastruktúrában, a mezőgazdasági berendezésekben.
Vannak olyan modern elektromos ívű pisztolyok is, amelyek inert atmoszférában működnek és spray-gáz-nitrogén vagy argonként használják. Ezekben a növényekben a bevonatokat aktív fémekből, például titánból és cirkóniumból kapják, a vegyiparban korrózióvédelemmel szemben.
A gáztermikus bevonatok bármilyen alkalmazásában nagy jelentőséggel bír a porlasztott felület előzetes kezelése, beleértve a mosó, zsírtalanító és csiszoló robbantási műveleteket. Az előkezelés hatással van a porlasztott bevonat tapadási szilárdságára a hordozóra. Számos esetben a porlasztást követően a gáz-hõvel bevont bevonatok további feldolgozási, nemezelési, mechanikai vagy fizikai-kémiai kezelésnek vannak kitéve, ami lehetõvé teszi a termék tapadásának és teljesítményének javítását. Jó eredményeket érnek el a fő hegesztési rétegeken át gázhővel ellátott bevonatokkal, amelyek általában durva felszíni megkönnyebbüléssel rendelkeznek.
A gáz-termikus permetezés folyamatát széles körben alkalmazzák számos más előnyben részesített előnnyel. Ezek a következők:
- annak lehetősége, hogy szinte bármilyen méretű és alakú tárgyakat bevonjanak;
- a lerakott anyagok és szubsztrátok legszélesebb skálája;
- a gázt termikus bevonatok alkalmazása nem okoz jelentős felmelegedést a kezelt felületeken;
- a porlasztott részek hőmérsékleti deformációi nincsenek;
- szerkezeti változások hiánya a munkadarab anyagában;
- magas gazdasági hatékonyság és környezetbarát.
Természetesen a leírt folyamatokat erőforrás-megtakarításnak kell tulajdonítani, mivel meghosszabbítják a berendezés élettartamát, lehetővé teszik a kiszáradt csomópontok helyreállítását, és nem helyettesítik újakkal. A funkcionális bevonatok használata lehetővé teszi drága anyagok megtakarítását, így a rész nagy részét olcsóbb fémekből készítik. A modern, automatizált gáz-termikus permetezésnek a gyártásba történő bevezetése lehetővé teszi a nagy teljesítményű, a modern technológiák követelményeinek megfelelő termékek előállítását.