Rolling technológia - kiváló minőségű acél, hengerhuzal, sínek és gerendák gyártása - fém raktár "ump"
Vasfémek gyártása
Rolling technológia (2. rész 3)
Nagy minőségű acél gyártása
A kiindulási anyag előállításához nagy méretű hengerüzemek (ábra. 6) használunk virágzik részén 300 × 300 mm, hossza 6 m. Blooms raktár rakodási daru egy fogadó rács 1 Nagyméretű malomban 500. Mivel vevő rostélyok virágzik esik egy rendszerindító fűtőhenger 2 kemencék. Módszertani kemencék fűtési virágzáshoz 3.
A gördülési hőmérsékletre felmelegített virágokat az emelőállványok tervezett csoportjának 4 adagoló görgős szállítószalagjába szállítjuk, amely négy munkaállványból áll, amelyek horizontálisan elrendezett görgők. Az első négy munkaállvány névleges átmérője 630 mm, a fennmaradó öt pedig 530 mm.
Szükség esetén a billentés a billentővel a merítési csoport előtt kerül. A tekercsek nagyolási csoportjának gördülése után a tekercs eléri az elülső végét az ollókon, és a következő munkaállásokon van elhelyezve. Minden munkaállvány három párhuzamos vonalban helyezkedik el - az első sorban öt munkaállomás található, a második sorban - a harmadik és a harmadik.
Átadása hengerállványhoz között végezzük a dolgozó görgős asztal, áll a párhuzamos vonalak - Chain átutalások minden sor 5. A gördülő egységek vannak telepítve billentők lehetővé felborulásának harangzúgás, 45 vagy 90 ° C.
Nagyméretű egy félfolyamatos mill 500 kapnak I-gerendák és csatornák № 10-20, sarkok № 8-16, egy kör átmérője 50 és 120 mm, a négyzet alakú keresztmetszet 50 × 50-100 × 100 mm, stb, függően a keresztmetszeti területe a kész A gördülés az első, a második vagy a harmadik vonal munkaállványainak egy csoportja után érhető el. Az egész gördülő körfűrész vágási hossza 6-6 m és 24 m, és mindegyik csíkot viszünk fel a bélyegző. A méretre vágott lapított továbbított hűtőszekrények és hűtés után vetjük alá egyengetése rolikopravilnyh gépek és prések, hideg vágás, szóló.
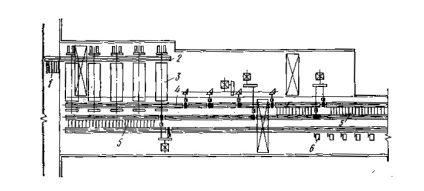
A malom éves átlagos kapacitása 1 millió tonna kész hengerelt termék.
Közepes minőségű acél gyártása
A kiindulási anyagként használt közeg-malom üres négyzet keresztmetszetű 150 × 150-200 × 200 mm, hossza 12 m. Az előformákat után ellenőrzés és tisztítás rakodódaru befogadására egyik rács (ábra. 7). Ahhoz, hogy a hő a tuskó meghatározott módszeres fűtési kazán 2. A fűtött tuskó gördülő hőmérsékletre audio feltolva görgős asztal és továbbítjuk hengersoron. A hengermű közvetlenül a töltőállomás után biztosítja az üresek gördítését.
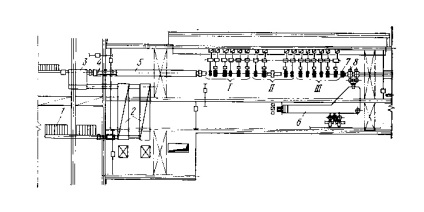
Ebben az esetben, az előformát kemencében melegítik 3 egy hengermű vonal durva vonalú stykosvarochnoy gép 4, melegítjük szakaszában kemencében 5 1250 ° C, és majd gördülő a görgős konvejor. A 450 hengerlőmő az I., a II. Közbenső és a befejező III munkacsoportok csoportjából áll. A nagyoló csoport hat, két tekercs állványból áll, amelyek közül kettő függőleges tekercsekkel van ellátva.
Görgők, csatornák és csíkok (szalagok) esetén a tekercsek horizontális elrendezését kombinált munkaállványokon használják. A tekercsek a munka áll vágják patakok box-kaliberű gyémánt rendszer - szögletes, ovális - tér és kaliberű kialakulásának gerendák, csatorna, szögek. Helyen hengerelt sebességgel 3-15 m / s vágják repülő ollók 7. csíkok letekerjük tekercs súlya legfeljebb 3 tonna felváltva működő két tárcsa 8 és továbbítani a szalag-típusú szállítószalag 6 hűtésére és kötelező.
Hosszú termékeket vágnak ollós ollóval a hossza szélességének megfelelően. Lehűlés után a tekercset kiegyenesítik, vágják az ollókra vagy körfűrészekre (gerendák, csatornák), címkével ellátva és a csomagolásra szállítják.
A malom éves kapacitása 1,4 millió tonna kész hengerelt termék.
Kis minőségű acél gyártása
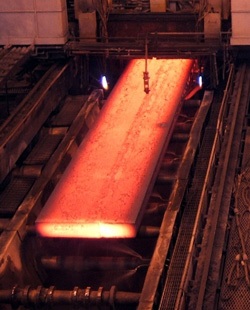
A kiindulási anyagot a könnyű-szakasz malomban 250 használ Négyzetek részén 80 × 80 mm, hossza 12 m. A raktárban készített gördülő tuskó daru munkadarab felvittük egy befogadó aprításra malomban 250. Mivel rendszerindító rostélyok munkadarab egyik oldalán befogadására görgős asztalra, amelyek szállítják a módszeres kemence.
A hengerlési hőmérsékletre felmelegített előgyártmányokat a kemencéből a görgős asztalra tolják ki, és a tartóállványok folyamatosan nagyolásra vannak állítva. Szükség esetén a munkadarab elülső vége le van vágva a malom nagyolócsoportja előtt elhelyezett repülő ollókon. A tekercseken a négyzet-ovális körrendszernek négyszögletes gyémánttal és négyszögletes gyémánttal vannak ellátva.
A malom az egyes munkaállványok egyedi tekercsének egy különálló villanymotorból való vezetésére szolgál. Köztes és befejező malom körébe tartoznak hengerállványhoz függőleges tekercs, amely szükségtelenné teszi a billentő tekercs. A fény-szakasz malom 250 hengerelt acél átmérőjű 10-30 mm, egy négyzet egy oldala 8-27 mm, 2-4 mm-es szalag vastagsága és szélessége 12-70 mm, és a sarkok 50 × 50 mm.
Miután az állványok befejező csoportjába gördültek, a kész hengerlést a tekercsbe vagy rúdhoz egy kétoldalas hűtőszekrénybe vezetik. Az állványok mindegyik befejező csoportjához négy tekercs és egy repülő olló található. Kerek acél, legfeljebb 25 mm átmérőjű és szalag acél sodrott, bekötött, bekötött és át a horog szállító.
A hengerlés többi részét vágó ollóval vágják a rudakra, és egy 125 mm hosszúságú kétirányú hűtőszekrénybe kerülnek. Hűtés után a gördülést ellenőrizni, válogatni, hosszra vágni, csomagolni és a raktárba küldeni.
A 250 malom éves termelékenysége 650 ezer tonna.
Huzalrudak gyártása
A kiindulási anyagot a használatra huzal malom 250 Négyzetek 60 × 60 mm-es, 12 m hosszú. A vizsgálat után és tisztítása a munkadarab tápláljuk rakodódaru rácsos hengermű amelyből az egy érkezett a felfogó henger fűtési újrahevítő kemence.
A kemencék üregének betöltése és előrehaladása tolófejjel történik; az 1180-1200 ° C-ra hevített előformák adagolását a kivetítő biztosítja. Az üregek eloszlását az első nagyolóállvány kaliberei szerint egy dob típusú elosztóval végezzük. A nyersdarabok forgalmazóját követően lyukasztók vannak felszerelve, amelyek szükség esetén vágják el a munkadarab elülső végét vagy a munkadarabot a malomban bekövetkező baleset során. A 250 folyamatos huzalháló három állványcsoportból áll: nagyolás, közbenső, kikészítés.
A nagyoló csoport első két állványának tekercsén a csiszolt doboz kaliberek áramai készülnek, amelyek biztosítják a jó vízkőmentesítést. A merevítő csoport többi állványának hengerén az ovális-négyzet rendszer kaliberei és a rombusz-négyzet készültek. Az ovális négyzetrendszer kalibereinek tekercseléseit a közbenső és befejező állványcsoportok tekercsére vágják.
Az utolsó befejező munkaállvány tekercsében egy ovális tekercs van beállítva, amely a krimpelés után 6,5-10 mm átmérőjű kör alakját adja.
A 12-30 m / s sebességű, vízhűtéses csöveken történő hengerlés a tekercsbe kerül.
Az állványok mindegyik befejező csoportjához két kazán van felszerelve. A huzalrúd kötélei a szállítóberendezésbe egy szállítószalaggal vannak ellátva és a horogkötő horgokra vannak szerelve. Lehűtés után a hengeres rudak rúdjait a visszahajtó gép eltávolítja a horog-szállítószalagból, két helyen vannak kötve és egy bálázógépbe táplálják. A modern speciális huzalos malmokban az utolsó munkaállásokban a gördülési sebesség ≥ 60 m / s.
A fém hőmérséklete az utolsó állvány után 1000 ° C.
A hengerlés után a méretek képződésének csökkentése érdekében, a finomszemcsés szorbitolszerkezet kialakítása érdekében a huzalhengerlő berendezések a rúd felgyorsított hűtésére szolgáló berendezésekkel vannak felszerelve, mielőtt zavargásokat vizsgálnak.
A vezetékes hengermű éves termelése 700-800 ezer tonna.
Sín és gerenda gyártása
A vasúti-nyaláb üzletek termelnek sínek súlya 75 kg-ig méterenként, I-gerendák akár 400 mm-es, csatornák, szög profilok legfeljebb 230 × 230 mm-es, a szádfal profil és a kerek rudak, amelyek átmérője 120-350 mm.
A vasúti gerenda billenője virágzik. A virág tömege 2-4 tonna, a virágzásokat rendszeres kemencékben melegítik.
A görgős síneket a 1180-1200 ° C-ra melegítik. A módszeres kemence végüvegén keresztül a krimpelő állvány adagoló görgős szállítószalagjába kerülnek. A krimpelő állványnál öt járatnál egy munkadarabot kapunk, amelynek durva sínje van.
A következő gördülő háromtengelyes állványnál 3-4 lépésben a keresztmetszet tovább csökkenthető és megközelíthető a vasúti formához. A sínnyaláb négy munkaállása lineáris (lineáris séma). Az utolsó munkaállvány két tekercs, benne van, egy lépésben, a végleges formát gördíti. Az egyik virágból 25 méter hosszúságú két sínek állnak rendelkezésre, a hosszmérőtől függően a sínek 12-14 lépésre vannak tekercselve.
A lerakó görgős asztalra a síneket 25 m körfűrész vágja le.
A felszínen a patak a befejező Caliber végre mélyedés (betűk és számok), amelyek a márka: a gyártó jelölése (karakter), acéltartalomnak, év, hónap, típus sín (P43, P50 ... P75), a kijelölés a hőkezelés típusa (És Izotermikus öregedés). Ezenkívül a vágás után az olvadási számot a szerszámra szorítják.
A 450-500 ° C hőmérsékletű darabokra darabokra vágott sínek lassú hűtést végeznek a kútokban vagy az izotermikus öregítésben. Továbbá a gyártósoron a síneket hőkezelésnek vetik alá. A vasaló keménységének a HB 320-380 határain belül kell lennie. A vasúti részlegben a sínek hideg állapotban vannak, a végeket szúrják és fúrják a lyukakat. A végső művelet a sínek végeinek nagyfrekvenciás keményedése.
A vasúti gerenda éves termelékenysége:
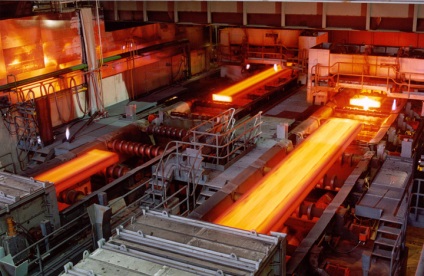
Speciális rendeltetésű malmok
A különleges gördülőállományok vasúti kerekeket és kötéseket, gömböket, különböző alakú forgóvázakat, fogaskerekeket, hajlított profilokat stb. Gyártanak.
A kerekek gyártása a következő technológiai műveleteket tartalmazza. A tíz-tizenkét oldalú ingot olyan részekre vágják, amelyek megfelelnek a kerék tömegének, és egyenként billentik fel.
A bemetszett rúdak elválasztása hidraulikus vízszintes présen 3 MN erővel történik.
A 950 és 1050 mm átmérőjű kerekek gyártásához a billet tömegének körülbelül 500 kg-nak kell lennie. Az előformákat 1200-1250 ° C-ra melegítik folyamatos forgó kemencékben.
A kármentesítést forgó lánccal végezzük, majd ezt követően hidraulikus préssel. Ugyanezen sajtolásnál a munkadarab az átmérő szerint van kalibrálva, amelyet a gyűrűkben lévő vázlat ér el, és a központi lyuk villogása. A munkadarabot 7,5 kN emelési kapacitással rendelkező padló-esztergáló gép segítségével mozgatják.
Átszúrása után a központi nyílás előformát egy hidraulikus présben erő 70 MN rábélyegezni a kerékagy, a lemezt, és a durva kerékabroncs.
Továbbá a gördülő malom a tárcsa, a perem feltekercselése és a kerék gerincének görgése. A végső műveletet egy hidraulikus présen végezzük 25 MN erővel. E művelet során a kerék megkapja az utolsó formát. Ez a művelet a két furat villogása és a bélyegzés kombinációja.
Később a kerék izotermikus öregedésnek van kitéve a kúthoz tartozó kemencékben. Ennek a műveletnek az a célja, hogy kiküszöbölje a nyáj kialakulását.
Lehűlés után a kerekeket vizsgálják, válogatják és keménységre tesztelik. Ezt követően végre megmunkálása kerekek forgácsoló gépek, edzés a perem és a gerinc, nyaralás kerekek kolodtsevoy kemencék, keménység teszt és válogatás. A kerekes hengerlővel működő műhely éves termelékenysége
350 ezer kerék. Különböző átmérőjű golyók előállításához nagy teljesítményű technológia magában foglalja a következő műveleteket.
A kezdeti hengeres billet, amelyet 1000 ° C-ra melegítenek, egy két tekercses hengerművel van felszerelve, csavaros kaliberekkel.
A munkadarab az egyik irányban forgó hengerek tengelye mentén van beállítva, és forgatás közben transzlációs módon mozog. A munkadarabot a csavaros kaliberek csúcsain vágják, a vágott darabokat karmantyúsan és golyóvá alakítják. A malom teljesítménye eléri a 150 golyót percenként. A rúd hossza mentén változó átmérőjű, kör alakú profilokat háromhengeres, keresztezett hengerléssel hengerítenek.
Az egyik irányban forgó hengerek tengelyei a gördülő tengellyel kapcsolatban 3-6 ° -kal billenthetők. Az 1000 ° C-ra melegített előformát tekercsekben állítjuk be.
A tengely körül forgatva a munkadarab a gördülő tengely mentén mozog. Egy adott programhoz a tekercseket közelebb hozza a munkadarab tengelyéhez vagy elvonja tőle. A hengerek megközelítését és visszahúzását a munkadarab tengelyétől egy hidraulikus présmechanizmus hajtja végre.
Keresztirányú spirális gördülés féltengelyeket gyárt az autók, billet perselyek, stb Elvileg lehetséges, hogy szinte minden forradalom. A gyártási alkatrészek pontossága magas, ami lehetővé teszi, hogy a megmunkálás során minimálisra csökkentsék a forgács forgácsát.
A fogaskerekek és a fogazott kerekek megkapja a meleghengerlés egy hengermű tekercs, amely képződik a hordó fogak és a kívánt profil a modul. A felfutási tuskó melegítjük és 1000 ° C, a fogak a hengerek vezetik be a szervezetbe az előforma, alkotó üregek és kényszerült fém kitölti a térfogata a bemélyedések a hengerek, a fogak formázó fejen.
Gördülő fogaskerekek és fogaskerekek gyártásakor nagy fémmegtakarítást érnek el finom megmunkálással.
A belföldi iparág elsajátította a termelést és gyártott gördülőmalmokat a menetes hengerléshez, a csövek gyártását bordákkal a külső felületen.
A vékonyfalú hajlított profilok széles körben alkalmazzák a mérnököket és az építkezést. A komplex keresztmetszetű vékonyfalú profilok gazdaságilag nemkívánatosak, ha folyamatos lerakódásból gördülnek, és egyes esetekben lehetetlen.
A vékonyfalú profilok gyártását többcsöves profilhenger alakító gépeken végzik.
A komplex keresztmetszet profiljának megszerzését fokozatosan hajlékony lemezes anyag érhető el kettős tekercselésű ketrecekben. A tekercsek hordóján kaliberek vannak vágva, amelyekben a lemez végleges hajlítását végezzük, amíg a kész profilt beszűrjük. A profil kilépési sebessége az utolsó állványtól akár 3 m / s is lehet. A lemezanyag vastagsága nem változik a profilalkotás során.
A technológiai folyamat a következő műveleteket tartalmazza. A szalag tekercs fel van szerelve az alvázra, és a végén a hajlítás a megfelelő gépen van beállítva. Profilok előállításához 0,5-20 mm vastagságú szalagot használjon. A következő lépés a csík elülső végének metszése és az előző tekercs csíkjának vége felé történő hegesztése. Így a folyamatot folyamatosan végezzük.
Hegesztési részek végei közötti a szalag, és egy folyamatos szakaszt hajlítási malomban meghajtó hurok szalag, amely a szalag betápláljuk a formázó hegesztés közben. A folyamatos tekercselő malom 20 vagy több munkatartóból áll, amelyekben a szükséges profilt fokozatos elasztikus-műanyag hajlítás képezi.
A profil alakjának megváltoztatásakor az alakító tekercseket kicserélik. A profilokat repedő ollóval (fűrészekkel) vágják fel mért hosszúságúra, és a végleges alakot egy megfelelően kalibrált malomban kapják.
Formázás előtt a csíkra kenõanyagot kell felhordani a profil felületi minõségének javítása érdekében, az elõkészített profilt pedig megkötés elõtt kenni kell, hogy megõrizzék.
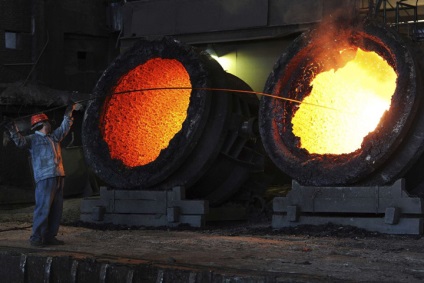
A hosszú termékek gördülőmalmai műszaki és gazdasági teljesítménye
Fémfelhasználás
A gördülési folyamatot fémes veszteség követi, a méretezés, a vágás, a forgácsok, a csupaszolás, az őrlés, a fúrás stb. Formájában.
A gördülőhellyel rendelkező késztermékek előállítására szolgáló fém fogyasztását a költségtényező becsüli meg. Határozza meg a gördülő virágok és lemezek fogyasztási tényezőjét.
A virágok és födémek fej- és farokrészeiből származó vágás eléri a 17,5% -ot, a fémveszteség pedig skála formájában 3%. Ennek következtében a kész lemezek súlya 20,5% -kal kevesebb, mint a hengerléshez kapott hengerek tömege, és 79,5%; a virágok (tábla) előállítására szolgáló fogyasztási tényező 100: 79,5 = 1,26.
A hosszú termékek előállításához szükséges fémfogyasztási tényezők a következők:
A hengermű típusa
Fém fogyasztási tényezők