Rendszergazdálkodás és kalibrálás
Irányítási rendszerek és nyomatékérzékelők kalibrálása
Eredeti cikk (PDF)
2. Minőségellenőrző rendszer és kalibrálás
Számos forrás azt olvassuk, hogy egy sorozatára DIN EN ISO 9000 és nőtte ki magát kapta a legelterjedtebb nemzetközi szinten, és ezért gyakran irányítási rendszerek működnek e szabvány szerint. Ezután jön minden szolgáltató számára, hogy az autóipar létfontosságú norma ISO TS 16949, amely tekinthető egy kiegészítője a szabványsorozat DIN EN ISO 9000 Először is, meg akarjuk nézni mind a minőség-ellenőrzési rendszer tekintetében az irányítási mérőműszerek. Ezután megnézzük, hogy mit keresünk a kalibrálás során. Ezt követően a nyomatékmérő műszerek helyes kalibrálásának normái és utasításai felé haladunk, a tudományos és technológiai fejlődés szintje szerint.
2.1 A mérőműszerek kezelése a DIN EN ISO 9001 szabványnak megfelelően
A mérési és vizsgálati módszerek a 7. szakasz "A termékek életciklusának folyamata" című szakaszban találhatók, és nem igényelnek nagy teret ebben a szabványban. A 7.6 alfejezetben megtaláljuk azokat a rendelkezéseket, amelyek szerint a mérőeszközök kezelését végre kell hajtani. E rendelkezések szerint rendszeresen kalibrálni kell mérőberendezéseinket. Abban az esetben, ha a mérőműszer a tűréshatárokon kívül esik, ki kell igazítani (beállítani). A kalibrálási állapotot fel kell tüntetni a mérőberendezésen. Pontos információ arról, hogy mit jelent a kalibrálás, például nem szerepel ebben a normatív dokumentumban. Csak az alfejezet végén a figyelmes olvasó a DIN EN ISO 10012-re hivatkozik, amelynek címe: "Mérési menedzsment rendszerek - Követelmények a mérésekhez és a mérőberendezésekhez". A DIN EN ISO 9004 "QMS - Ajánlások a teljesítmény javítására" sem találunk semmilyen jelentős jelzést erre a célra.
2.2 A mérőműszerek kezelése az ISO TS 16949 szerint
A fentiek szerint a DIN EN ISO 9001 a normatív dokumentum alapja, ezért a DIN EN ISO 10012-re vonatkozó megjegyzés megtartja hatását itt. Ezen túlmenően vannak olyan követelmények a mérőberendezések kezelésére, mint például a következő bejegyzések:
- A nemzeti szabványok nyomon követhetősége
- Mérés és műszaki követelmények a kalibrálás után
A külső laboratóriumokban végzett kalibrálásnak továbbá a következő követelményeknek kell megfelelnie:
- A laboratóriumnak bizonyos tevékenységi körrel kell rendelkeznie (ebben az esetben - nyomaték)
- A laboratóriumnak akkreditáltnak kell lennie a DIN EN ISO / IEC 17025 szabványnak megfelelően
3. DIN EN ISO 10012 Mérési irányítási rendszerek. A folyamatok és létesítmények mérésére vonatkozó követelmények
A költségvetés tartalmazza a mérőműszer összes releváns befolyási értékét, például a kalibrálási mérések bizonytalanságát, a hőmérséklet hatását, a driftet, az interferenciát stb. A mérési bizonytalanság ilyen mérlegét a szokásos táblázatos számítási programban lehet összeállítani. A forgatónyomatékra vonatkozó nemzeti szabványok a Braunschweig Szövetségi Fizikai Technikai Hivatalában (Physikalisch Technischen Bundesanstalt, PTB) vannak. Ezen előírások segítségével az erő pillanatának tartományai teljesen le vannak fedve, hézag nélkül, 1 mN · m - 200 000 N · m.
A Német Kalibrációs Szolgálat (DKD) DKD-4-ben a metrológiai nyomon követés elemeit pontosan leírták, és a 6. ábrán láthatóak és bemutatták. 1 rész.
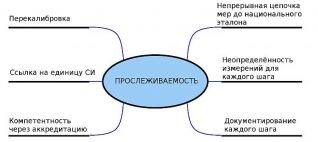
Ábra. 1: A metrológiai nyomon követhetőség elemei
Az akkreditált kalibráló laboratórium kompetenciáját az akkreditált területen kívül a DKD szolgáltatás engedélyezi, ha ugyanazon mérési érték kérdése. például nyomaték (szakmai kompetencia).
Kalibráló Laboratórium Lorenz Messtechnik GmbH a regisztrációs számot DKD- K-37801 saját precíziós szabványok, a mérési bizonytalanság, amelyet által meghatározott kalibrációs PTB (ábra. 2). A szabványokat rendszeresen újra kalibrálják a PTB-ben, és a saját kalibrálóállomás ellenőrzésére és nyomonkövethetőségére szolgálnak, amelynek mérési bizonytalanságát ezek a szabványok határozzák meg, mint 1 · 10 -4. A kalibrálási tanúsítványok biztosítják a kalibrációs állvány és szabványok metrológiai nyomon követhetőségét.
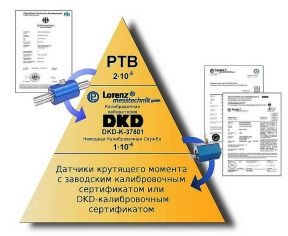
Ábra. 2: Folyamatos szabványlánc a PTB-ből a mellékelt érzékelőhöz
Meghatározás: A műveletek, amelyek a mérőműszert készenléti állapotba hozzák.
A nyomatékérzékelőkre vonatkozó folyamat a 3. ábrán látható. 3. Először a nyomatékérzékelő "memóriája" több előfeszítéssel törlődik. Ezt követően a beállítási folyamat nulla értékről indul, és a névleges nyomaték beállítása után. A sikeres kiigazítás után maga a hitelesítési folyamat is megkezdődhet.
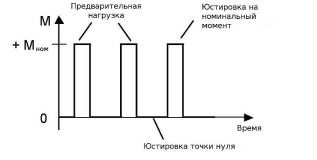
Ábra. 3: A nyomatékérzékelők összehangolása
A Lorenz Messtechnik GmbH meghatározása a DKD-re támaszkodva: több termékmutató meghatározása és dokumentálása.
A nyomatékérzékelőket az 1. ábra szerint határozzuk meg. 4 a következő értékeket, amelyeket az új, mellékelt érzékelőre vonatkozó protokollban rögzítettek: A nullpont mért értékeit, az Mn 50% -át és 100% -át eltávolítják és dokumentálják. Ezek az értékek kiszámítják az érzékelő zérusjelét, linearitását, hiszterézisét és érzékenységét, és dokumentálva vannak a protokollban.
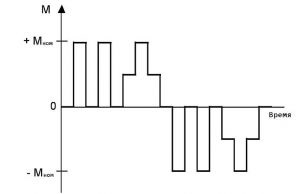
Ábra. 4: A nyomatékérzékelők ellenőrzésének folyamata
A beállítási eljárást, valamint a nyomatékérzékelők ellenőrzését nem írja le vagy magyarázza semmilyen szabályozási dokumentumban. Tehát az érzékelők gyártói nagyon különbözőek lehetnek itt.
5. Nyomatékérzékelők kalibrálása
A nyomatékérzékelők kalibrálása az ismert eljárásoknak vagy normáknak megfelelően történik. Csak a jobb oldali kalibrációra korlátozzuk magunkat.
5.1 Kalibrálás a DIN 51309 szerint
Nézzük meg részletesebben a DIN 51309 szerinti kalibrálást a jobb oldali nyomatékkalibrálás 8 fokozattal. Jellemzően a terhelési fokozatokat a névleges nyomaték Mnom 10%, 20%, 30%, 40%, 50%, 60%, 80% és 100% -ában választják ki.
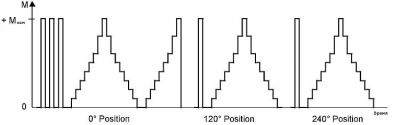
Ábra. 5: A DIN 51309 szerinti kalibrálási folyamat 8 lépésben
Három előzetes terhelés (5. ábra) névleges nyomatékkal, 8 pontot mérünk növekvő terheléssel, és végül 8 pontot csökkenő terheléssel. Ezután a nyomaték növelése egy sor, amely meghatározza az érzékelő ismételt pontosságát.
Ezután az érzékelő 120 ° -kal elfordul a mérő tengelyéhez képest. Az érzékelő előretöltött egy névleges forgatónyomatékkal, majd a forgatónyomaték lépésenkénti növelése és csökkenése következik.
A szenzor következő forgása 240 ° -ban a végső mérési készlettel, amint az a grafikonon látható, kiegészíti a mérési pontok felvételét a jobb oldali nyomaték kalibrálásához.
A 6. ábra az egyszerű kalibrálási folyamatot mutatja az 1-5.
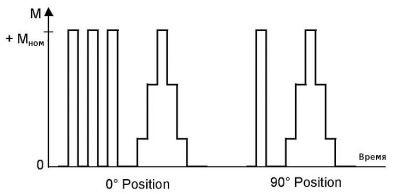
Ábra. 6: Nyomatékérzékelő kalibrálása három mérési lépésben
Amint a diagramon látható, sokkal kevesebb mérési pontot távolítanak el. Ezenkívül lehetőség van a 0 ° -os érzékelő pozícióban lévő második emelkedési sor nélkül is, mivel a megismételt pontosság mindig magasabb összehasonlítható pontossággal egyenlő. Ezután az érzékelőt csak egyszer kell elforgatni a berendezésben. Ezzel a kalibrálással az érzékelő erőssége az 1-5. Osztályba sorolható, bár a mérések bizonytalansága alacsony lehet. Ez az oka annak, hogy ez a kalibrációs módszer nem vonatkozik a jobb mérőeszközökre. Az osztályok alatt sokszor az érzékelő "pontossága" értendő, amely azonban nem feltétlenül felel meg a valóságnak. Ezért továbblépünk egy olyan másik utasításra, amely nem igényli ezt az osztályelosztást.
5.2 A nyomatékérzékelők kalibrálása a VDI / VDE 2646 szerint
Ezzel a kalibrálással a nyomatékmérők osztályai szerint nincs eloszlás, mint a DIN 51309 esetében. Minden mért értéknél a mérési bizonytalanságot kiszámítják és jelzik.
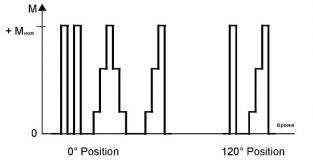
Ábra. 7: A nyomatékérzékelők kalibrálása három mérési fázisban a VDI / VDE 2646 szerint
A kalibrálás elindul, amint az a 2. ábrán látható. 7. ábra, az érzékelő minimális előfeszítésével, névleges forgatónyomatékkal, valamint fokozatosan növekszik és csökken a terhelés. A következő egy újabb emelkedő sor lesz az ismételhető pontosság érdekében. Ezt követően az érzékelő a mérő tengelye körül elfordul, és előfeszítés után egy sor nyomatékkiemelés következik. Ezt a kalibrálást természetesen nagyszámú lépésben, például 8 lépésben végezhetjük, mint például a DIN 51309 esetében (lásd a 8. ábrát).
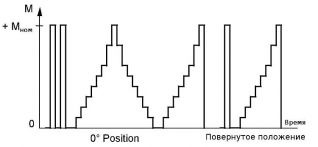
Ábra. 8: Nyomatékérzékelő kalibrálása 8 mérési fokozatban
Ha tudjuk, hogy a relatív pontosság az előző kalibráció, vagy ha meg lehet állapítani egy kalibráló laboratórium típusú vizsgálatok által dokumentált statisztikai eljárás, lehetséges, hogy lemondunk a második érzékelőt. A kalibrálás csak egy pozícióban összehasonlító pontosság nélkül nem engedélyezett kalibrálással, és nem felel meg a technikai szintnek.
5.3 A hatások megosztása a mérések bizonytalanságára a megfelelő részekre (tényezők).
A kalibrációs eredményt mind DIN 51.309 és VDI / VDE 2646 egy mért érték sorozatot növekedését és csökkenését a pillanat való eltérés, ami lehet százalékában a végső értéke a beállító funkció, mint a 9. ábrán látható figyelembe venni tényezők (alkatrészek) befolyásolva a mérések bizonytalanságáról. Ez nagy felbontással és stabilitással rendelkező mérőerősítőt jelent.
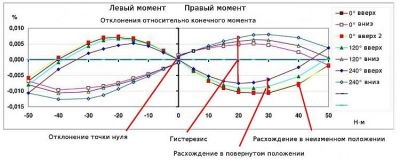
Ábra. 9: A nyomatékérzékelők kalibrálásakor a nyomatékhoz viszonyított tipikus eltérések a DIN 51309 szabvány szerint
Az első inline pozíciótól a 0 ° pozícióig az ismételhető pontosság a mért értékek eloszlásaként határozható meg. A forgatott helyzetek mért értékei a saját diszperzitásukkal járulnak hozzá az összehasonlító pontosság meghatározásához. A fordított löket (hiszterézis) terjedését a növekvő és csökkenő sorok határozzák meg. A terhelési sor végén maradt nullpont eltérése is számít.
Annak érdekében, hogy a mérések bizonytalanságát ne csak a rögzített mért pontok esetében határozzuk meg, meg kell határozni az interpolációs eltérést a 10. ábrán látható módon.
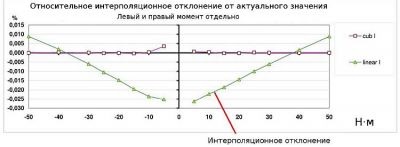
Ábra. 10: Interpolációs eltérés lineáris és köbös polinom esetén a kalibrálás során
Ezenkívül figyelembe kell venni a használt kijelzőt annak felbontásával és a kalibráló berendezés mérési bizonytalanságával. A mérés bizonytalanságát nem szabad összetéveszteni a pontossággal. A DIN 55350 szerint a precizitást minőségi meghatározásnak kell tekinteni a mérési eredmény közelítésének nagyságára a jelenlegi értékhez képest.
5.4 Besorolás a DIN 51309 szerint
Miután gyakran olvassuk a nyomatékérzékelők osztályozását, röviden itt vegyük figyelembe ezt a paramétert.
Osztályokra van szükség ahhoz, hogy egyszerűen összehasonlíthassuk a különböző gyártók nyomatékmérő berendezéseit egymással. A besorolás paramétereit a kalibrációs mérések bizonytalanságának részei határozzák meg. A besorolás alapja az, hogy minden osztályra és minden paraméterre korlátozó értékek vannak. Ha ezt az értéket túllépték, a mérőeszköz egy magasabb osztályba kerül. Minél magasabb az osztály, annál több paraméter befolyásolja a mérések bizonytalanságát. Ez azonban nem vonatkozik a 3 kalibrálási lépéssel történő kötelező osztályozásra.
5.5 Szabványok (normák) és utasítások (utasítások) a nyomatékérzékelők számára
A kalibrálási normákat és szabályokat megerősített módszerekre, gyártói utasításokra és kalibrációra osztják fel az ügyfél igényei szerint. A megerősített kalibrálási módszereket az elismert hatóságok (szakemberek csoportja) írják elő a normákban vagy az utasításokban (például a DKD-ben). Annak érdekében, hogy olcsóbb kalibrálási módszereket kínáljunk, a gyártók belső módszerei vannak. De általában nem ismeri fel, és nem állapítja meg a mérések bizonytalanságát a technikai szintnek megfelelően. Amint azt már bemutattuk, a mérések bizonytalanságának megállapításához szükség van olyan értékek meghatározására, mint az ismételhető pontosság, az összehasonlító pontosság, a visszafutás, a nulla pont eltérés és az érzékelő interpolációs eltérése. Ellenkező esetben a kalibrációs módszer nem ismerhető fel megerősítve. Az alábbi grafikon (11. ábra) a leírt kalibráció legfontosabb formáit és a nyomatékra vonatkozó követelményeket tartalmazza. A K betűvel jelölt módszerek a műszaki szint szerint kalibrálhatók. A P betűvel jelölt módszerek ellenőrizzék az érzékelő mérését és műszaki adatait, és tesztelési bizonyítványok formájában dokumentálják őket.
A K által jelzett kalibrációkat tovább osztják a DKD és a gyári kalibrálási (WKS) kalibrációkra.
Ábra. 11: A nyomatékérzékelők kalibrációs szabványai és szabályai
5.6 DKD kalibrálás a gyári kalibrálással szemben (WKS)
Mint láttuk, a mai súlyos kalibráló laboratóriumok, hála az érvényes szabványok és előírások, lehetőség van arra, hogy végezzen gyári kalibrációs (WKS) a DIN EN ISO 9000 és DIN EN ISO 10012. Mivel annak érdekében, hogy még képesek kalibrálni, ma már nem kalibráció szükséges a. Ha kalibráló laboratórium akkreditált további nyomatékot, egy ilyen laboratórium végzi a minőségirányítási rendszer (MIR) szerint tanúsított ISO TS 16949, korrekt DKD- kalibráció és gyári kalibrációs (WKS) tükröző kalibrációs szakaszban az egyes mérési bizonytalanság. DKD kalibráló laboratórium akkreditált területei lesznek nagy mérési műszaki hozzáértéssel, és nagyon jól képzett személyzet, amely a jelenlegi fejlettségi szinten a tudomány és a technológia. Ezenkívül ezek a laboratóriumok közvetlenül a PTB alatt állnak a hierarchiában.
A DKD és a WKS kalibrálása közötti különbség az, hogy a WKS gyári kalibrálásához a VDI / VDE 2646 egyszerűsített formában alkalmazható. Így a kalibrálás könnyebb és olcsóbb, de az aktuális technikai szinten is helyes. A WKS kalibrációs tanúsítvány gyártása azonban a kalibráló laboratórium feladata. Amikor DKD kalibrációs maga kalibráció és kalibrálási tanúsítványok végzi DKD követelmények és ellenőrzi a szolgáltató, ami jóval magasabb munkaerő-ráfordítás dokumentálása az ilyen típusú kalibrációs.
A nyomatékmérő berendezés felhasználójának biztosítania kell, hogy a gyári kalibrálás kalibrációs kalibrációs tanúsítványa jelzi a mérések bizonytalanságát, valamint a mérési bizonytalansághoz vezető alkatrészeket. Mivel a VDI / VDE 2646 szerint a kalibrációk a mérési bizonytalanság feltüntetése nélkül használhatatlanok. Ezenkívül fel kell tüntetni az alkalmazott kalibrálási módszert. Ha a kalibrálási módszer "támaszkodik" vagy "kalibrál a gyártó utasításai szerint", akkor ellenőrizni kell, hogy ez a kalibrálás általában megfelel-e a jelenlegi technikai szintnek. A gyártói garanciával kapcsolatos nagyobb bizonyítási erővel, amely valójában mindig referencia-érzékelő használatával jár, szükséges a DKD kalibrálása. Ezek a kalibrálási tanúsítványok nemzetközi szinten elismertek, és nagy bizonyító erejűek a garancia ügyben.
Egységváltó
Kezdeti érték:
Jelentése: