A galvanikus királynő Galván titkainak zsírtalanítása
A galvanikus bevonatok minősége nagymértékben függ az előkezeléstől, különösen az alkatrészek felületének zsírtalanításától (lásd "A galvanizálás minőségének okai").
A galvanikus bevonatok gyakorlatilag megismétlik a felületi mikrorégiót, így a dekoratív bevonatok és a korrózióállóság csak a felület alapos zsírtalanításával érhető el.
Az alkatrészek felszíni szennyeződésének jellege eltérő lehet. A hőmér- sékletet, a korróziós termékeket, a szulfidokat és az oxidfóliákat maratással eltávolítják.
Zsírok, tartósítózsírok, polírozó paszták, emulziók formájában keletkező szennyeződések eltávolítása a felület zsírtalanítása során történik. A zsíros szennyező anyagok felületének zsírtalanításának módját természetük határozza meg. Az ásványi eredetű zsírok (polírozó paszták, kenőanyagok, ásványi olajok), amelyek nem oldódnak vízben, eltávolítják, ha a felületet szerves oldószerekkel zsírtalanítják. A növényi vagy állati eredetű zsírok, amelyek nem oldódnak vízben, hanem kölcsönhatásba lépnek a lúgok vizes oldatával, eltávolítják a felületet az alkálifémsók oldatainak zsírozásával, így oldódó szappanokat képeznek.
A képzés során a legszélesebb körben alkalmazott zsírtalanítási módszereket veszik figyelembe.
A felület zsírtalanítása szerves oldószerekben.
A szerves oldószerek nagyon toxikusak. Csak speciális felszereléssel és a biztonsági előírások betartásával használható (lásd "Biztonságos galvanizálás"). Jelenleg a legszélesebb körben használják a nem éghető oldószereket a felület zsírtalanítására: triklór-etilén, tetraklór-etilén, szén-tetraklorid és freon.
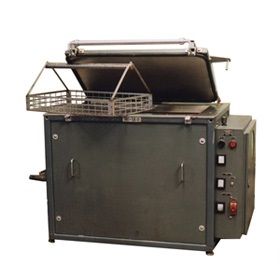
Zsírtalanító alkatrészekhez
A triklór-etilén a legtöbb fém felületét zsírtalaníthatja. acél, réz, nikkel és ötvözeteik. A nagy reaktivitás miatt a vízzel nedvesített részek zsírtalanítása nem megengedett, mivel a triklór-etilén bomlik sósavgőz képződésével, ami a berendezés korrózióját okozza.
Triklór-etilénben alumínium és titán alkatrészek zsírtalanítása nem engedélyezett. mert az oldat felmelegszik és bomlik mérgező vegyületek felszabadításával.
A leginkább egyetemes fluor-tartalmú szénhidrogének (freon F-113). A felület zsírtalanítását olyan berendezésen végezzük, amely kizárja a gőz belépését a légkörbe.
Az alkatrészek felületének szerves oldószerekben való zsírtalanításának folyamata nem biztosítja a szennyező anyagok teljes eltávolítását, ezért szárítás után az alkatrészeket kémiai vagy elektrokémiai zsírtalanításhoz vezetik.
Az alkatrészek felületének kémiai zsírtalanítása.
A kémiai zsírtalanítás az, hogy a lúgos zsírok hatására elszappanosítják és átviszik az oldatba, és az ásványolajok különleges felületaktív anyagok jelenlétében emulziót képeznek.
A felület kémiai zsírtalanítására szolgáló megoldások lúgokat, foszfátokat, szilikátokat, különböző felületaktív anyagokat (szantanolt, DS-10, szintetamid-5 stb.) Tartalmaznak. A lúgosság fokozata három csoportra tagolódik: erősen lúgos, közepesen lúgos és enyhén lúgos.
Az alumínium, cink és ón részek zsírtalanításához alacsony koncentrációjú lúgos oldatokat használnak, nagy koncentrációban - az acél részek felületének zsírtalanításához.
A könnyű ötvözetek felületének zsírtalanítására szolgáló oldat összetétele g / l:
Nátrium-hidroxid 8-12
Nátrium-foszfát 20-50
Nátrium-folyékony üveg 25-30
Hőmérséklet 40 - 70º, idő 3 - 10 perc
Az összes kémiai vegyi felület zsírtalanító oldata 20-30 g / l "Labomid" vagy "Detalin" vagy "Impulzus" tisztítószert tartalmaz, 60-80 ° C hőmérsékleten, a feldolgozási idő 3-10 perc.
Ahogy a zsírtalanító folyamatot, a felszínen a cseréje alkalmazott szerves oldószerek kémiai zsírtalanítás detergensek CM-1, labomid-203, ML-52 és mtsai., Amelyek magukban foglalják a tripolifoszfátok, SYNTANOL DT 7, szóda, akrilsulfaty.
Zsírtalanítására az acél felülete alkalmas detergensek: CM-1, CM-2, CM-3, labomid-203, ML-52, stb mennyiségben, 15 - 30 g / l, a hőmérséklet 50 - 70 C ° a kezelési idő 5 - 20 perc. .
Zsírtalanítására felületei réz, ezüst, titán, nikkel, Invar és a cink az optimális detergens: ML-51, LME-1, OC-1, CM-2, ML-52, labomid-203 és mások koncentráció 60-80 g. / l, a feldolgozási idő 3 - 15 perc, 60-80º.
Zsírtalanítási az alumínium ötvözet felületén végezzük mosószerek: CM-2, CM-5, KME-1, ML-52, MS-8 labomid-203 koncentrációban a 10 - 20 g / l. A hőmérséklet 50 - 60º, az idő 5 - 10 perc.
Elektrokémiai zsírtalanítás.
A fémfelület elektrokémiai zsírtalanítása hatékony módszer a vékony zsíros filmek tisztítására, amelyeket más módon nehéz eltávolítani. Amikor kitett aktuális hidrogén ionok csökken a katódon a buborékok formájában elválasztásának elősegítésére olajcseppek zsírtalanítására felületi részek. Azonban, a hidrogén abszorpció előfordulhat részeinek acél felületek, ahol a vékony falú és a rugók széttöredezzen, így gyakran alkalmazott módszer a zsírtalanítás kombinált: 5-8 perc a katód, 1 - 2 percen át az anód.
A rézből, cinkből, alumíniumból és ötvözeteikből készült alkatrészek felületének elektrokémiai zsírtalanítása csak a katódon történik. Az alkatrészek felületének elektrokémiai zsírtalanításának tisztítási sebessége sokkal magasabb, mint a felület kémiai zsírtalanítása, a minőség jobb. A hátrány az elektrolit alacsony disszipációs kapacitása, ezért nagyon nehéz a komplex részek felületének zsírtalanításának folyamata.
Elektrokémiai felületi zsírtalanítás elektrolit összetétele:
nátrium-hidroxid - 20 - 40 g / l, nátrium-foszfát 20-40 g / l, nátrium-karbonát -20 - 40 g / l, hőmérséklet 60 - 80 ° C, DC = 2 - 10 A / dm 2, míg a katód 3-10 perc, az idő az anódon 1-3 perc.
Biztonsági okokból szükség van a hab eltávolítására az elektrolit felületéről az elektrokémiai zsírtalanítás során. mivel robbanásveszélyes gázt (hidrogén és oxigén keverék) tartalmazhat, és nem tartalmaz sok emulgeálószert és felületaktív anyagot. A hőmérséklet növekedése felgyorsítja a felület zsírtalanításának folyamatát, növeli az oldat elektromos vezetőképességét, ami növeli az áramsűrűséget.